Wire rope are safety-critical components extensively used in many industries, such as in industrial production, tourist cable cars, mining, metallurgy, shipyard, and elevators. Wire rope is a heavily loaded component, and long-term continuous operation eventually result in corrosion, abrasion, broken wires, pitting and fatigue, which decrease the loading strength of the rope, and can cause accidents, resulting in property damage and injury. In many cases failure of a wire rope could lead to expensive damage to equipment or even to loss of life.
To avoid such failures, current methods of wire rope inspection are usually carried out visually and in some industrial practices wire rope are often replaced at regular intervals without testing. American research has shown that there are 10% wire rope in use which their ultra limit over 15%, they are in dangerous state. There are 2% wire rope in use which their ultra limit over 30%, they are in extremely dangerous state. More than 70% wire rope which are force to replaced have little or no strength loss. The traditional damage detection method is a low efficiency, time-consuming, and unreliable method. The development of a fast, non-destructive and automatic detection technology is therefore necessary.
The main non-destructive testing(NDT) methods employed for wire rope inspection include electromagnetic detection, ultrasonic guided wave(UGW) evaluation, radiation testing, eddy current inspection, and optical detection. However, designing a precise detection device that can qualitatively and quantitatively determine the type of flaws when operating in severe environments.
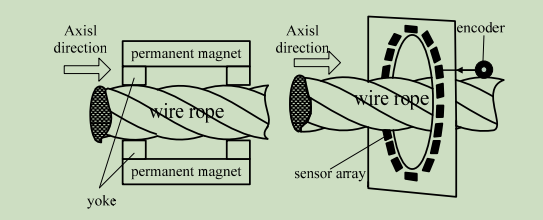
Electromagnetic detection methods are commonly employed for the NDT of wire rope. TST wire rope flaw detection system adopts EM sensor technology for the ferromagnetic objects. The principle of TST technology is magnetizing the wire rope with magnets. Wire rope consists of flexible ferromagnetic steel wires twisted in a helix structure around a hemp core. After the magnetization of wire rope was completely homogenized by the magnetization device, a weak magnetic field existed on the surface of the rope, which was stable over a short period(the data acquisition operation could be implemented over the following week without magnetizing the system again). Sensor catches the magnetic signals to detect the rope flaws. This detection system is non-contact and non-invasive which prolong the service life of test device.
This inspection system offers a high accuracy and light weight. TST sensor range reaches 30mm, so the service life of the equipment is longer than that of traditional devices since it suffers from less friction due to the high lift-off distance.
Wire rope defects include two main types: the loss of metallic area(LMA), local faults(LF). The focus of the test is to detect the EM field signal induced by the target and recognize the featured flaw signals through regulating and detecting process. The advantage of such a high sensitivity and high resolution is that all different types of flaws on the target will be detected from internally and externally. TST advanced sensor technique ensures that the noise signals are effectively screened out so that we could develop an accurate pattern recognition model for system automation and intelligent computer evaluation
TST Company will continue to be a leader of non-destructive flaw detection of steel wire ropes.
More Than Safer
prev: Operational requirements for operators in wire rope flaw inspection
next: Conditions of ensuring the accuracy of wire rope testing